What Are Different Types of Bending Systems For I-Beam Rolling?
Are you curious about the various types of bending systems used for I-beam rolling? Look no further! This blog post will deeply dive into the different methods and techniques used to bend I-beams with precision and efficiency. So buckle up, grab a cup of coffee, and let's explore together! From pyramid rolling to section bending, get ready to discover the wide range of options available in today's industry.
Types of Bending Systems
Hydraulic Benders
Hydraulic benders are one of the most popular types of bending systems for I-beam rolling. They offer high accuracy and repeatability, making them ideal for use in a wide range of applications. Hydraulic benders can be used to create both simple and complex shapes and can be easily programmed to produce precise results.
Mechanical Bender Arms
Mechanical bender arms are machines used to bend and form metal into various shapes. These devices allow for the precision bending of complex parts without human intervention. Bender's arms are often found in factories and workshops as they are highly efficient, reliable, and accurate pieces of equipment.
Mechanical bender arms offer an easy way to produce high-quality components quickly at a low cost. They can be used on various materials, such as steel, aluminum, copper, or brass. Many come with integrated safety features to prevent injury or damage to the workpiece being bent. With their versatility, mechanical bender arms can replace manual labor in many applications where time is critical, or there is no access to skilled labor.
CNC Machining Centers
CNC Machining Centers are a great choice for I-beam rolling because they provide precise, accurate bends that conform to exact specifications. The entire process can be automated and controlled with precision with CNC machines thanks to computer numerical control (CNC) software. This allows operators to set up the bend parameters accurately before starting each cycle to ensure repeatability and increase efficiency.
The machine's cutting tools also help maintain tight tolerances during each operation, which is especially important when working with I-beams. Additionally, CNC machining centers allow even complex shapes and profiles to be produced quickly while still providing high-quality results every time.
What to Consider When Choosing a Bending System?
When it comes to choosing a bending system for I-beam rolling, you'll need to consider a few things. First, you must decide what material you'll be working with. There are systems designed for use with steel and aluminum beams, so ensure you get the right one for your needs.
Next, you'll need to consider the size of the beams you'll be working with. Make sure you choose a system that can handle the beam size you'll be using. There are systems designed for use with beams up to 12 inches in width and those that can accommodate wider beams.
Finally, you'll need to consider the type of bends you'll make. Some systems allow for simple 90-degree bends, as well as those that can create more complex shapes. Choose a system that will give you the flexibility to create the kinds of bends you need.
Conclusion
I-beam rolling is an important process for creating flexible and durable parts. The different types of bending systems are key to this process, as each system has its own advantages and disadvantages. Knowing which type is best suited for your project will be essential to achieve the desired results from your projects. We hope this article has provided you with a better understanding of the different bending systems available for I-beam rolling so that you can make an informed decision about which one will work best for your needs.
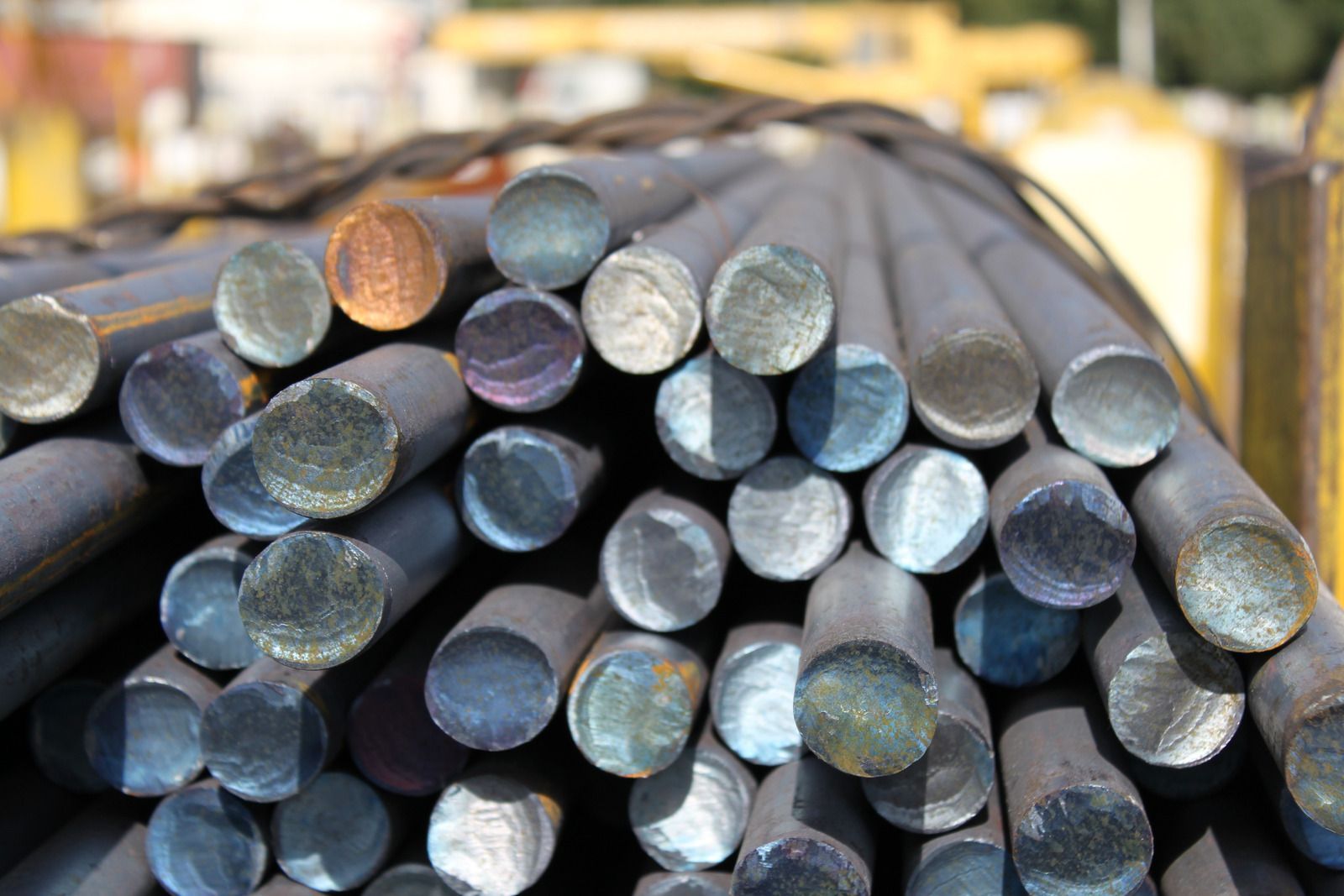