Latest Advancements in Channel Rolling for Precision And Durability
Have you ever wondered how modern construction achieves those seamless curves in metal structures? Or how intricate metal designs maintain both their beauty and strength? The answer often lies in channel rolling, a crucial aspect of metal fabrication. Let's dive into the world of channel rolling and discover how its latest advancements shape the future of precision and durability in metal works.
Understanding Channel Rolling
Channel rolling is a metalworking process where metal is passed through a series of rollers to bend it into a specific shape, such as a channel or a cylindrical form. This process is fundamental in creating parts for various industries, from construction and automotive to aerospace. With the advancement of technology, channel rolling has evolved, offering greater precision and durability in the final products.
6 Advancements In Channel Rolling
1. Technological Breakthroughs in Precision
One of the most significant advancements in channel rolling is the introduction of CNC (Computer Numerical Control) technology. CNC machines have revolutionized channel rolling by allowing for extremely precise bends and cuts. These machines are programmed with exact specifications, ensuring that each bend is consistent and accurate. This level of precision is essential, especially in industries where even a minor deviation can lead to significant problems.
2. Enhanced Durability with New Materials
Developing new, stronger materials has also played a vital role in advancing channel rolling techniques. High-strength steels and alloys are now being used to withstand more significant stress without deforming. This enhancement in material science increases the durability of the rolled channels and allows for more ambitious designs and applications.
3. Increased Efficiency with Automation
Automation has brought about a significant increase in efficiency in the channel rolling process. Automated channel rolling machines can operate continuously with minimal human intervention, speeding up production times and reducing the likelihood of errors. This automation ensures a more consistent product and allows for quicker turnaround times for projects.
4. Eco-friendly Practices in Metal Fabrication
Sustainability is a growing concern in all industries, including metal fabrication. Advances in channel rolling technology have also focused on reducing environmental impact. It includes using recyclable materials and energy-efficient machines, which not only help conserve resources but also reduce the overall carbon footprint of the production process.
5. Customization and Versatility
Another exciting development in channel rolling is the ability to produce more customized shapes and sizes. Modern machines can handle a broader range of materials and thicknesses, allowing for more versatility in design. This flexibility enables architects and designers to explore unique structures and forms in their projects.
6. Ensuring Quality and Safety
With the increased precision and durability offered by these advancements, there is a notable improvement in the quality and safety of the final products. It is especially important in construction and transportation, where the strength and reliability of metal components matter a lot.
Looking to the Future
The future of channel rolling looks promising, with ongoing research and development in materials science and machine automation. These advancements will continue pushing the boundaries of what's possible in metal fabrication, leading to even more innovative and resilient structures in the coming years.
The latest advancements in channel rolling are transforming how we work with metal. From increased precision and durability to eco-friendly practices and automation, these developments are enhancing efficiency and opening up new horizons in design and construction.
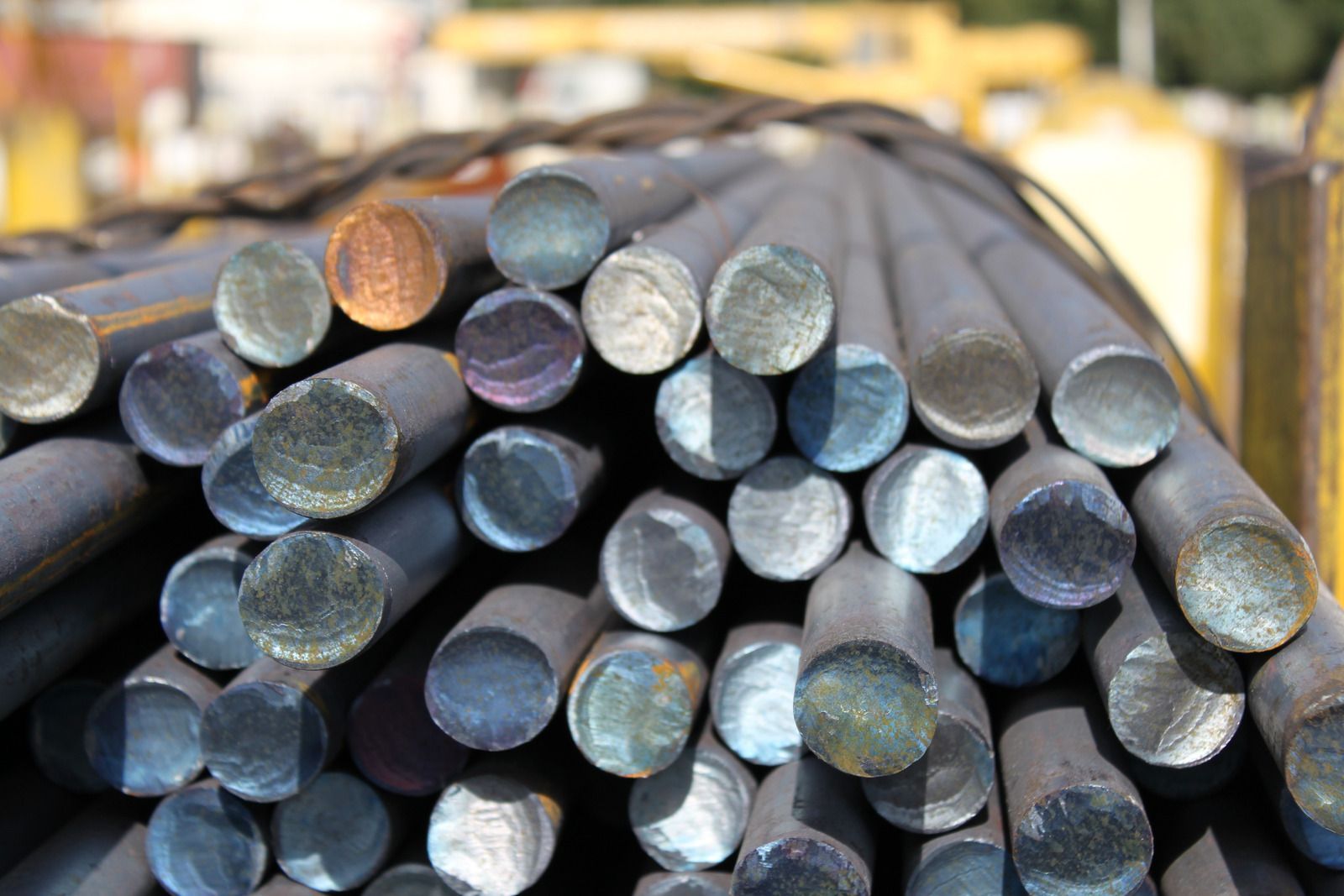